
“수백 차례 충돌 시험을 반복하고, 결국 원하는 강도가 나올 때까지 제철업체와 연구를 거듭해 제품을 만듭니다.”(김익수 현대·기아차 연구개발본부 재료개발1실장)
○ 車업계, 초고장력 강판 경쟁
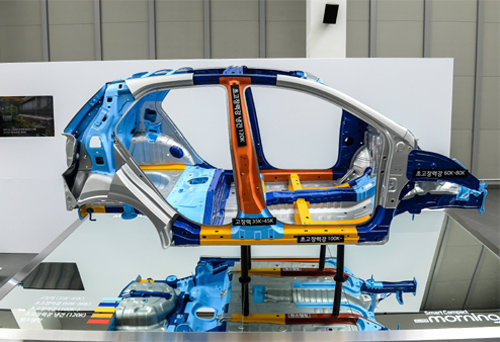
여러 분류 기준이 있지만 현대·기아차는 30kg/mm²급을 일반 강판, 35∼50kg/mm²급을 고장력 강판, 60kg/mm² 이상을 초고장력 강판으로 분류한다. 60kg/mm²급이란 사방 두께 1mm의 가느다란 강판 가닥이 60kg의 무게를 견딜 수 있는 만큼의 강도를 뜻한다. 김 실장은 “초고장력 강판 적용 비율과 충돌 안전성은 거의 비례한다”고 말했다.
기아차는 이달 신형 모닝을 출시하면서 초고장력 강판 적용 비율을 22%에서 44%로 늘렸다. 한국GM 쉐보레도 포스코 초고장력 강판을 경차 스파크에 38.7%를 적용했다. 특히 모닝이나 스파크 같은 경차는 안전에 대한 우려가 더 많아 이를 불식시키기 위한 업체 간의 경쟁이 치열하다.
김 실장은 “초고장력 강판은 1970년대 이미 개발됐지만 워낙 단단해 열처리, 성형, 냉각 조절 등이 어려워 2000년대 초반부터 상용화됐다”고 말했다. 현재 현대·기아차가 만드는 승용차에는 초고장력 강판이 평균 50∼54% 적용된다.
○ 분자 단위부터 연구… 신기술 도입 박차
소비자들이 ‘더 단단한 쇳덩어리’ 정도로 알고 있는 초고장력 강판을 차체에 적용하기 위한 과정은 몹시 복잡했다. 남양연구소에서는 초고장력 강판을 분자 단위부터 연구하고 있었다.
연구소 투과전자현미경분석실에서는 초고장력 강판을 세포 샘플처럼 얇게 잘라 분자 배열을 살펴보고 있었다. 오승택 현대·기아차 연구개발본부 강판재료개발팀장은 “강판을 0.0002mm 두께로 잘라 딱딱한 요소와 연한 요소가 적절히 배열됐는지 살피는 과정”이라고 말했다. 연구원이 들여다보고 있는 현미경 가격만 20억 원이 넘는다.
금속물성시험실에서는 강판 조각을 인장시험기에 넣고 잡아당기는 실험이 한창이었다. 120kg/mm² 강도의 초고장력 강판 조각을 기계가 천천히 잡아당기자 3분 뒤 ‘딱!’ 소리와 함께 강판이 찢어졌다.
초고장력 강판은 단단한 특성 때문에 적용 비율을 늘리는 것이 쉽지 않다. 원하는 모양대로 만들려면 크랙(쪼개짐)이나 스프링백(성형을 하기 전 상태로 돌아가려는 현상) 등의 문제를 해결해야 한다. 강판끼리 이어 붙이는 용접도 일반 강판이나 고장력 강판보다 고난도의 기술이 필요하다.
최상의 적용 비율을 찾는 것도 과제다. 오규환 현대·기아차 연구개발본부 강판재료개발팀 책임연구원은 “차체를 100% 초고장력 강판으로 만들면 충돌사고 시 충격을 탑승자가 전부 받아 오히려 사망 위험이 높아진다”고 설명했다. 단단히 버텨줘야 할 부위와 찌그러지며 충격을 흡수하는 부위가 정교하게 나누어져야 한다는 뜻이다. 대형사고 때는 소방대원이 차체를 절단하거나 뜯어내야 할 때도 있다. 초고장력 강판은 절단이 쉽지 않아 남양연구소는 소방대원들에게 강판의 특징을 설명하는 자리를 마련하기도 했다.
해외 기술을 도입하기 위한 경쟁도 빨라지고 있다. 지금은 두께가 서로 다른 초고장력 강판들을 레이저로 용접해 이어 붙이는 방식(TWB)을 쓰는데 독일 업체는 하나의 초고장력 강판을 부위마다 두께가 다르게 성형하는 기술(TRB) 특허를 가지고 있다. 무게를 줄이고 강도를 높이는 기술이다. 현대·기아차도 이를 도입하기 위해 기술 협의 중이다. 신형 모닝 차체를 설계한 이재혁 현대·기아차 연구개발본부 스트럭처 설계1팀 책임연구원은 “안전한 미래차를 위한 소프트웨어가 자율주행과 커넥티드 기술이라면 하드웨어의 핵심은 초고장력 강판”이라고 말했다.
화성=이은택 기자 nabi@donga.com